株式会社ミューチュアル
日本ジェネリック製薬協会 賛助会員の株式会社ミューチュアルでございます。
当社は創業以来、日本の製薬、化学、化粧品等の業界の皆様に支えて頂き、約75年の歳月を歩んでまいりました。今まで、ありがとうございます。
この場をお借りして、弊社の創業からの歴史、現在の取り組み、環境・排出ガス抑制も含めた当社の取り組みをご紹介させて頂ければと存じます。
当社は1949年(昭和24年)に創業、以来75年間にわたり、製薬・化学・化粧品業界向けに、製造にかかわる設備の製造、販売、保守、エンジニアリングを行っています。
2024年4月に、弊社内組織を一新し、従来、営業部門とエンジニアリング部門に分かれていた組織を1つの専門組織へと改編。製薬業界に対応した窓口をファーマエンジニアリング部とし、化粧品業界に対応した窓口をコスメエンジニアリング部として、今まで以上にラインを含めたエンジニアリング提案が可能な組織となりました。
そして昨今、社会や業界も含めたグローバルな傾向として、排出ガス抑制や原材料の削減といった環境負荷への取り組みを行う事が急務とされています。この中で弊社がご提案できる取り組みや実績をご紹介させて頂きます。
【PTP包装機】
弊社にて、開発・製造を行っているPTP包装機は、その歴史は40年前に遡ります。簡単に歴史を振り返りますと、1980年に真空ドラム成型方式のPTP包装機を開発し納入、1987年PPフィルムに対応した平板成型方式のPTP包装機を開発し納入、2000年に弊社独自の成型方式「完全部分加熱成型」方式のPTP包装機を開発し納入し現在に至ります。
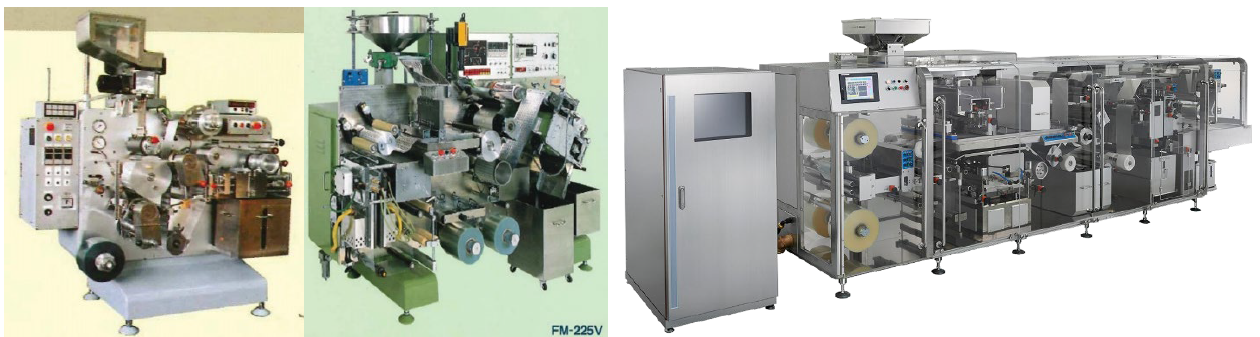
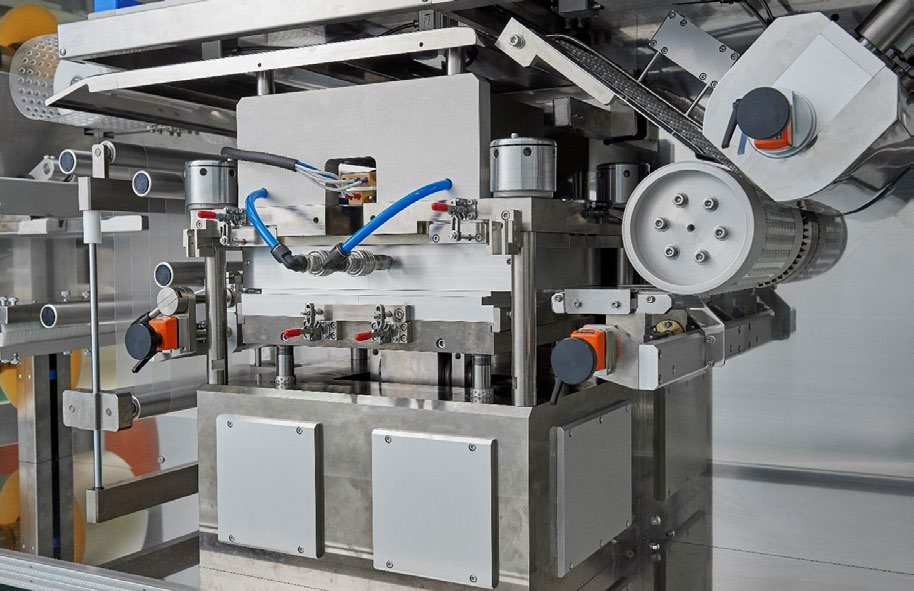
完全部分加熱成型方式のPTP包装機には、他社方式と加熱・成型方式が異なり、下記のような大きな利点を持っております。
1.加熱と成型が1つのステーションにて、行われ、成型する部分のみを加熱している為、電力消費量が大幅に減少、打ち抜き後のカールが大幅に減少
2.加熱板と成型が1つのステーションの為、フィルム搬送によるエネルギーロスが無い、機械停止後の、リスタート時の熱不良によるフィルムロスが無い
3.成形ポケットの天面、側面のフィルム厚をタッチパネルにて、コントロールが可能
4.金型を交換する事により、樹脂フィルムから両面アルミフィルムでの成型を簡単に切り替える事が可能
又、従来ボトムフィルム250μmの厚みを150μm(実績値)の薄いフィルムを使用する事も可能です。
この成型方式の違いだけで、
・樹脂使用量を従来比:約40%削減(自社比)
・温室効果ガス排出量:約40%削減(自社比)
を実現しております。
更に、機械停止後のリスタート時の熱不良によるフィルムロスが無い事から、上記+αでのフィルムロスの大幅削減を実現しています。
【カートナー】
通常のカートナーでは、電力消費量のほとんどが、熱可塑性糊に付随したヒーター等により消費されていますが、包材メーカー殿とのコラボレーションにより、熱可塑性糊を使わずに、改ざん防止効果がある封緘方式「ロックカートン」方式を考案しました。これにより、大幅な電力消費量の削減や熱可塑性糊特有のメンテナンス等が無い方式での封緘等を行うことが可能となります。
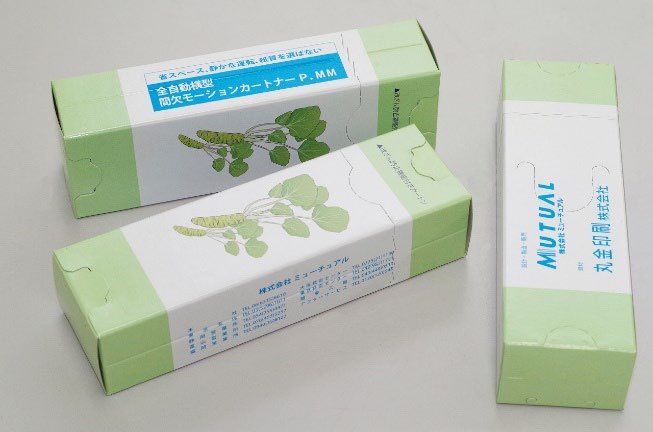
今後も、環境への取り組み、資材削減にも今まで以上に取り組みを行い、提案して参ります。
皆様からの色々なご指摘やご相談を通して、業界の発展や環境貢献をして参りたいと考えておりますので、よろしくお願い致します。
